Vat Photopolymerization is AM technology that produces 3D objects by curing photopolymer liquid resin using light waves.
Contents covered in this article
What is Vat Photopolymerization?
Vat Photopolymerization is a type of additive manufacturing technology that produces 3D objects by selectively curing photopolymer liquid resin using light-activated polymerization.
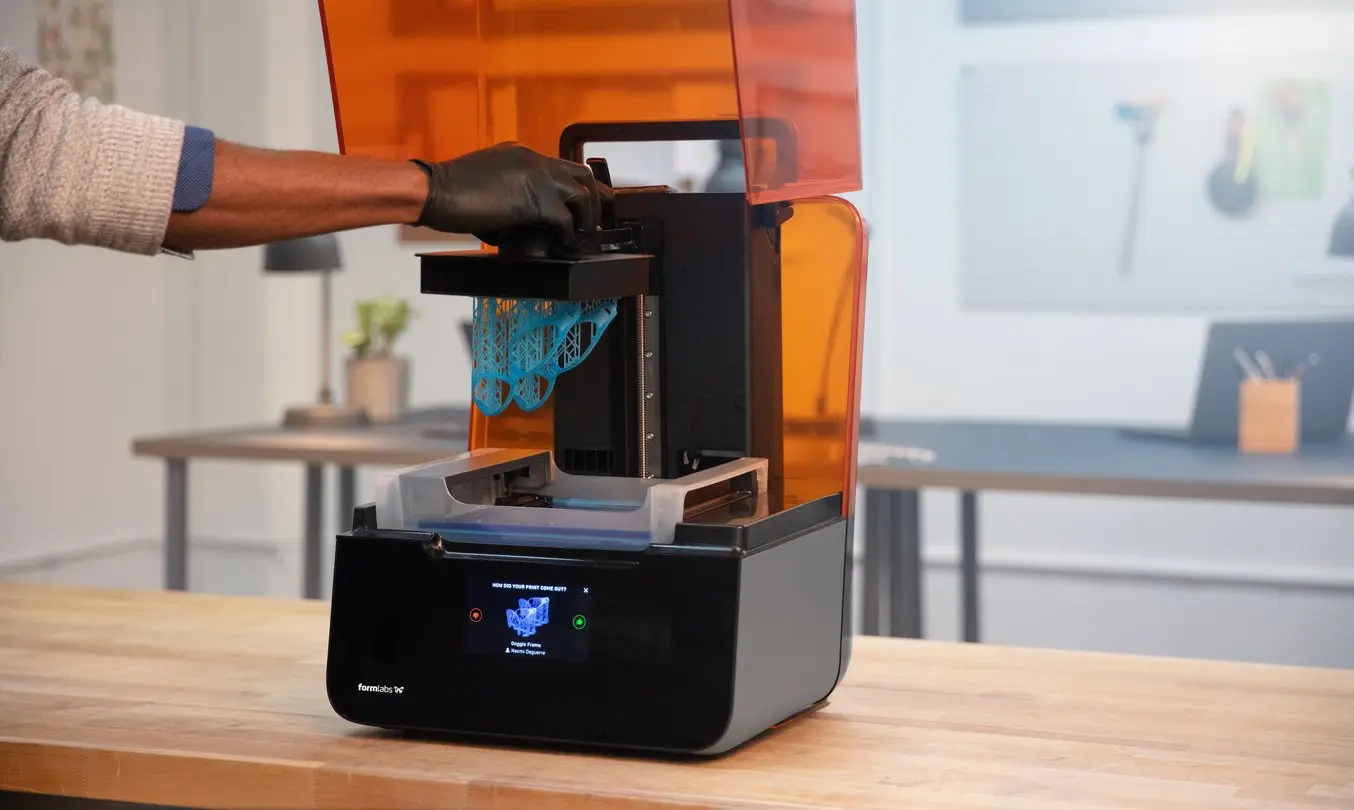
A photopolymer, also known as light-activated resin, is a polymer that changes its properties when exposed to light, often in the ultraviolet or visible region of the electromagnetic spectrum, causing its molecules chain to link. Stereolithography (SLA), the first patented and marketed AM process, is a vat photopolymerization technology.
Dr Hideo Kodama, a Japanese researcher, created the contemporary layered stereolithography technique in the early 1970s, employing ultraviolet radiation to cure photosensitive polymers. Chuck W. Hull invented the term stereolithography after patenting the technique in 1986 and establishing a company called 3D Systems to market it. Hull characterised the approach as printing small layers of an ultraviolet-curable substance in a series to create 3D things.
How does VAT photopolymerization work?
Special resins known as photopolymers are used as the printing medium in all forms of vat photopolymerization printers. When exposed to specific wavelengths of light, the molecules of liquid photopolymers quickly bond together and cure into a solid form, a process known as photopolymerization. Most 3D printers that use vat photopolymerization keep liquid photopolymer in a container or vat, with the build platform partially submerged at the liquid’s surface. The printer directs a light source to selectively cure the liquid photopolymer into a solid layer using information from a CAD file. The build platform is then re-submerged in the leftover resin, and the process is repeated for the subsequent layers until the design is entirely produced.
Vat photopolymerization types
The three main types of vat photopolymerization are:
- Stereolithography (SLA): SLA uses a laser to trace the cross-sections of an object on the surface of a vat filled with photopolymer resin. The laser hardens the resin to form solid layers. SLA is known for high resolution and smooth surface finishes.
- Digital Light Processing (DLP): DLP employs a digital light projector to flash entire layers at once, rather than tracing them. The projected image selectively cures the resin in a pattern corresponding to the layer, which speeds up the printing process compared to SLA.
- Liquid Crystal Display (LCD): LCD-based printing uses an LCD screen to mask a UV light source, exposing entire layers simultaneously similar to DLP. The LCD screen controls where the UV light hits, curing the resin in precise patterns. This method is often faster and less expensive, though it may not achieve the same fine resolution as SLA.
VAT photopolymerization applications
Vat polymerization methods are good for generating finely detailed pieces with a smooth surface finish. As a result, they are perfect for jewellery, low-run injection moulding prototypes, and a variety of dental and medical applications. The brittleness of the generated pieces is one of the key constraints of vat polymerization.
Advantages and disadvantages of VAT photopolymerization
Advantages of VAT photopolymerization
- A high degree of detail, precision, and overall quality
- The process is rather rapid
Disadvantages of VAT photopolymerization
- Costly in comparison
- Typically, they must be post-cured for an extended period to get significant strength from them
- Lack of photo-resin material choices
- Inadequate strength and durability
- After printing, resins can still be affected by UV Light
- Resins can warp and bend over time
Stereolithography (SLA)
Stereolithography is an additive manufacturing technology that builds three-dimensional parts layer-by-layer using a laser to cure liquid resin.
What is Stereolithography (SLA)?
Stereolithography is an additive manufacturing technology (3D printing process) that falls under the VAT photopolymerisation category. Vat photopolymerisation is one of the seven types of additive manufacturing technologies.
SLA stands for Stereolithography, an additive manufacturing technology that builds three-dimensional models layer-by-layer using a laser to cure liquid resin.
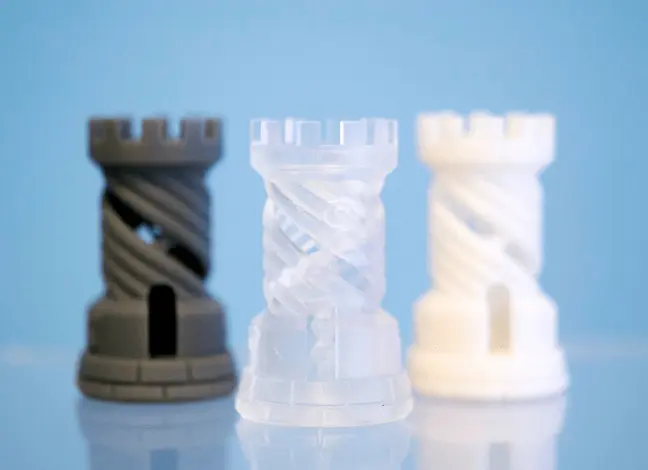
SLA involves laser curing of a liquid photopolymer resin into the desired shape. This process is possible because the photopolymer, as the name suggests, contains a compound called photoinitiators that reacts when the laser light is applied.
Since the laser light is a focused UV beam, it is possible to cure a specific portion of the liquid photopolymer. This feature makes it possible to generate a layer of the cross-section of the desired model on the X-Y plane. Therefore, repeating the process along the Z-axis results in a solid 3D model.
Materials | Photopolymer resins – thermosets |
Support | Always required ( Part design depended) |
Common layer thickness | 0.025 – 0.1 mm (0.001″ – 0.004″) |
Dimensional accuracy – Desktop | ± 0.5% (lower limit: ±0.10 mm (±0.004″) |
Dimensional accuracy – Industrial | ± 0.15% (lower limit ± 0.01 mm (±0.0004″) |
Typical build volume – Desktop | Up to 145 x 145 x 175mm (5.8″ x 5.8″ x 7″) |
Typical build volume – Industrial | Up to 1500 x 750 x 500mm (60″ x 30″ x 20″) |
How does Stereolithography (SLA) work?
SLA printer overview
A traditional SLA printer consists of the following:
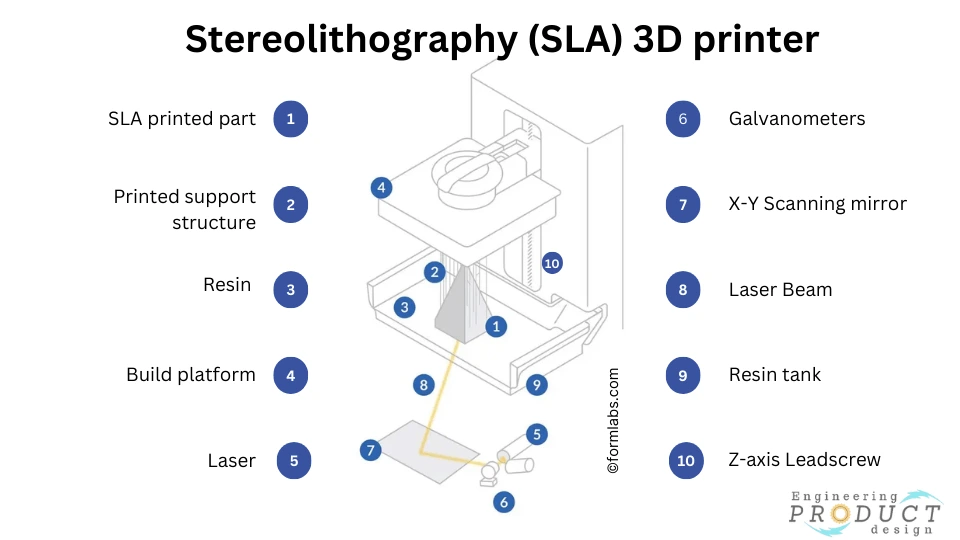
- A resin tank containing the liquid photopolymer
- A build platform connected to the moving Z-axis typically uses a lead screw. This platform holds the printed part as it goes through the SLA process. The Z-axis layer height dictates the verticle print resolution.
- A laser shines the beam via mirrors to move the laser beam along the X-Y plane.
While this is the traditional configuration, it is essential to highlight that some printers use the upside-down or inverted SLA process. The figure above shows an upside-down type of printer configuration.
Stereolithography (SLA) process steps
Creating a 3D model through SLA takes the following steps:
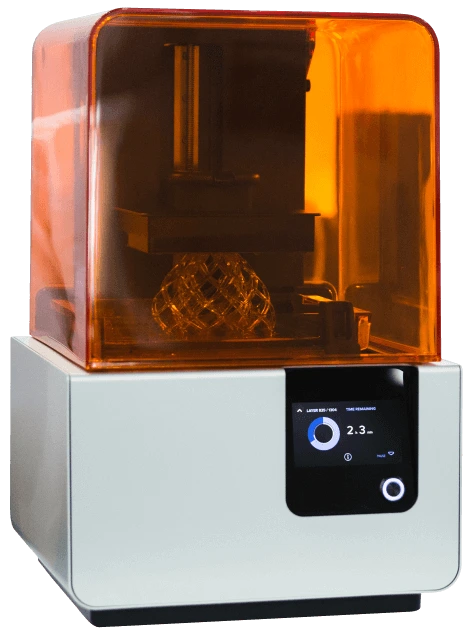
- The resin tank is filled with the photopolymer.
- The building platform is positioned at the highest possible point, ensuring a thin photopolymer layer covers it.
- Using the instructions provided by the software, the printer focuses the laser beam upon the corresponding surface area while moving across the X-Y plane to generate the desired layer.
- The laser cures the photopolymer until the layer is solid, thus forming the cross-section of the model.
- The building platform moves down so a new layer of liquid photopolymer covers the cured layer.
- The printer repeats steps 3-5 until the model is complete.
- The resulting part is removed from the printer, dried, and cleaned using ultrasound and alcohol. At this point, the operator must remove any support structures.
Advantages and disadvantages of Stereolithography
What are the advantages of Stereolithography?
- Reusable material – It is possible to use the portion of liquid photopolymer (not cured) that remains in the tank for further printing. This characteristic reduces material consumption.
- Tight tolerances – SLA can achieve tolerances as low as 0.01mm (0.0004″)
- Complex geometries – SLA can generate models with complex geometries, including oblique surfaces, without compromising the print quality.
- Smooth finish – SLA prints come out with smooth surface finishes directly from the printer. This feature reduces the need for further surface treatments.
- Large parts – Industrial SLA printers make it possible to 3D print components with sizes up to 1500 x 750 x 500mm (60″ x 30″ x 20″).
What are the disadvantages of Stereolithography?
- Non-functional prototypes – SLA prints are usually fragile, so they are not as adequate as functional prototypes.
- Photosensitivity – Given the nature of the process, SLA prints are sensitive to sunlight. It means the mechanical and visual properties can degrade if exposed to the sun.
- Required support structures – SLA requires support structures for all prints, no matter their geometry. This requirement impacts the amount of material needed. It also increases production times since postprocessing to remove these structures is necessary.
- Initial costs – The initial investment required to produce SLA prototypes may be high. At the industrial level, SLA machines can range between 100,000 and 400,000 US dollars, depending on their capacity. Regarding materials, the range is between 50 and 400 US dollars per litre, depending on the properties needed.
Stereolithography materials
What materials can be used for SLA printing?
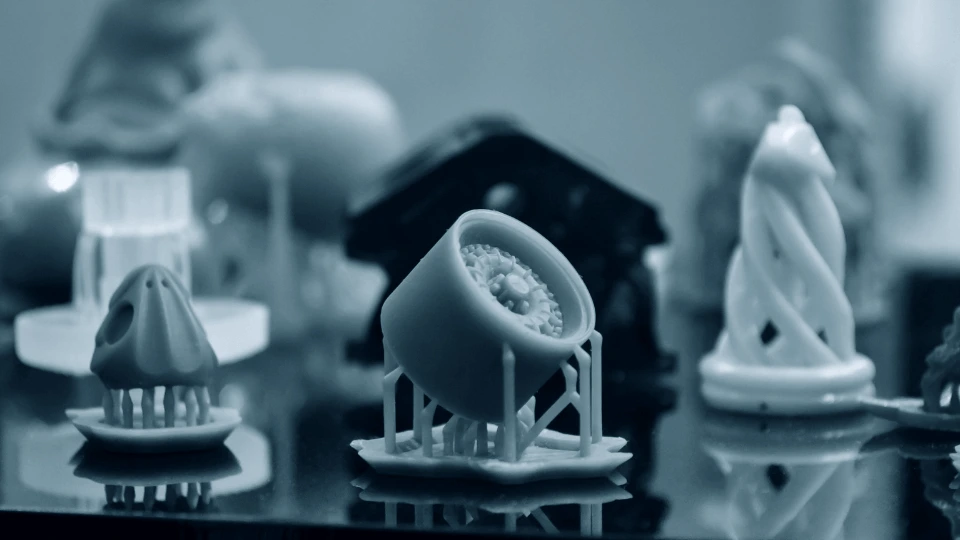
There are different types of liquid photopolymer resins, known as light-reactive thermoset materials, for SLA. Each option provides specific properties. The most common materials used in SLA include:
- Standard resin – Standard resin is the cheapest and offers a smooth surface finish. However, the print is usually fragile. Standard resin is a top option for rapid prototyping.
- Clear resin – As the name suggests, this resin results in translucid parts, but postprocessing is required to achieve this feature. Mechanical properties are similar to the standard resin, and it is also great for rapid prototyping, especially in fluid or lighting applications, given the translucid characteristic.
- High-detail resin – This material is similar to the standard resin. The main difference in this one is that it offers a higher degree of accuracy (lower tolerances) but comes at a higher price.
- Tough and durable resin – As the name implies, this material offers higher toughness and durability. Mechanical properties are similar to other strong materials like ABS or PP. According to 3DS, some SLA prints made with these materials have a tensile strength of 55.7 MPa and a modulus of elasticity of 2.7 GPa. Such properties make these materials engineering-level resins.
- Castable resin – The main properties of castable resins are that they work well with highly complex geometries. They also offer very smooth surface finishes. Moreover, these resins leave almost no residue after burnout. As a result, these are considered the best option for mould patterns and products like jewellery.
- High-temperature resin – Also known as heat-resistant resins, these materials can withstand very high temperatures with a heat deflection of up to 300°C (572°F). Therefore, these resins are the option when fabricating parts exposed to high temperatures, such as casting and thermoforming tooling.
- Flexible resin – The resulting part made with this type of resin is similar to one made with rubber, thus offering high elongation at break and a low tensile modulus. This feature makes it great for applications where compression or bending is required. However, dimensional accuracy is a limitation of this material.
- Dental and medical resin – This type of resin has similar properties to others but with a significant difference in biocompatibility.
Direct Light Processing 3D printing
When compared to SLA, Direct Light Processing (DLP) uses a very similar process of creating components. The primary distinction is that DLP employs a digital light projector screen to display a single picture of each layer all at once. Since the projector is a digital screen, the picture on each layer is made up of square pixels, resulting in a layer made up of little rectangular bricks known as voxels. For some items, DLP can achieve quicker print speeds than SLA since each full layer is exposed all at once, rather than tracing the cross-sectional area with a laser.
What is digital light processing 3D printing?
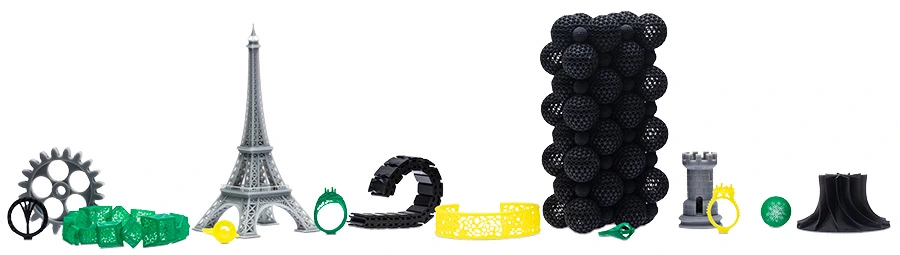
Direct Light Processing (DLP) is a 3D printing technology that uses a digital micromirror device (DMD) to project and selectively cure light onto a photosensitive resin. Developed by Texas Instruments, DLP precisely manipulates millions of tiny mirrors to direct light, creating detailed layers of a 3D object. The process involves the exposure of each layer of resin to UV light, causing it to harden, and successive layers are built up to form the complete object. DLP is known for its speed and accuracy and is popular for applications requiring high resolution and fine details, such as in prototyping and dental industries.
How does a DLP 3D printer work?
Direct Light Processing (DLP) is a 3D printing technology that utilises a digital micromirror device (DMD) to project light and cure a photosensitive resin. Here’s how it works:
- Preparation: A 3D model is sliced into digital layers using specialised software. These layers guide the projection of light in the printing process.
- Resin Exposure: A vat is filled with liquid photopolymer resin. The build platform is submerged slightly into the resin, just above the bottom.
- Light Projection: The DMD, containing millions of tiny mirrors, directs light from a UV or visible light source onto the resin. Each mirror corresponds to a pixel in the 3D layer image, tilting to reflect light in a pattern that defines the layer’s shape. The light selectively cures (hardens) the resin where it is projected, forming a solid layer.
- Layer Formation: Once a layer is cured, the build platform or the vat moves down, allowing fresh resin to cover the previous layer.
- Repeating Process: The process repeats for each layer until the entire object is built.
- Post-Processing: The printed object may require washing to remove uncured resin and curing under additional light to strengthen the material.
Pros of Direct Light Processing (DLP)
- High Resolution: DLP can produce intricate details and smooth surface finishes, making it suitable for precision applications like dental and jewellery.
- Speed: The technology projects entire layers simultaneously, faster than point-by-point methods like SLA (Stereolithography).
- Versatility in Materials: DLP can work with various resins with different properties, including flexible, tough, and biocompatible materials, offering various application possibilities.
Cons of Direct Light Processing (DLP)
- Limited Build Volume: Compared to other 3D printing technologies, DLP printers typically have smaller build areas, restricting the size of the objects that can be printed.
- High Material Cost: The specialised photopolymer resins used in DLP can be expensive, leading to higher operational costs, especially for large prints.
- Post-Processing: Printed parts often require additional steps such as washing, curing, and removing support structures, which add to the overall time and complexity of the printing process.
Continuous Direct Light Processing (CDLP)
Continuous Direct Light Processing (CDLP) manufactures parts in the same way as DLP does. It does, however, rely on the build plate’s constant motion in the Z direction. This results in quicker build times since the printer does not have to stop and extract the component from the build plate after each layer is generated. This process is also known as Continuous Liquid Interface Production or CLIP.
- Manufacturer – Carbon3D, EnvisionTEC
- Material – Standard, tough, flexible, transparent, & castable resins
SLA vs SLS
Stereolithography (SLA) and Selective Laser Sintering (SLS) are additive manufacturing technologies that utilise lasers to build 3D objects layer-by-layer.
However, they have some differences that are worth highlighting.
- Materials used – While SLA uses UV light to solidify a liquid resin in specific areas to form the desired 3D shape, SLS involves selectively melting a layer of powdered material with the laser to create a solid object.
- Build speed – SLS is a quicker process than SLA. This capability is a significant advantage of SLS over SLA since it can print more parts over the same period. It also makes SLS a better option for rapid prototyping.
- Precision – SLA offers the possibility of achieving tighter tolerances than SLS.
- Support structures – While SLA always requires support structures to build the model, SLS does not require any support structures since the powder surrounding the build supports any overhanging geometry.
- Mechanical properties – As mentioned above, SLA parts are usually fragile and do not serve as functional parts. On the contrary, SLS parts offer improved mechanical properties that make them tough enough to work as functional prototypes.
Recommended references
- Jacobs, P. F. (2012). Stereolithography and Other RP&M Technologies: From Rapid Prototyping to Rapid Tooling. Society of Manufacturing Engineers.
- Kochan, D. (2007). Stereolithography: Materials, Processes and Applications. Springer Science+Business Media.
- Fidan, I., Loh, H. T., & Jahan, A. (2012). Stereolithography: Materials, Processes, and Applications. McGraw-Hill Education.